Hey, welcome to this article, Here we will understand the Origin of Lean Six Sigma, How it started by Motorola, the evolution, and foundations of lean six sigma. How lean and six sigma combinations transformed the organizations. so let’s start…
Lean six sigma
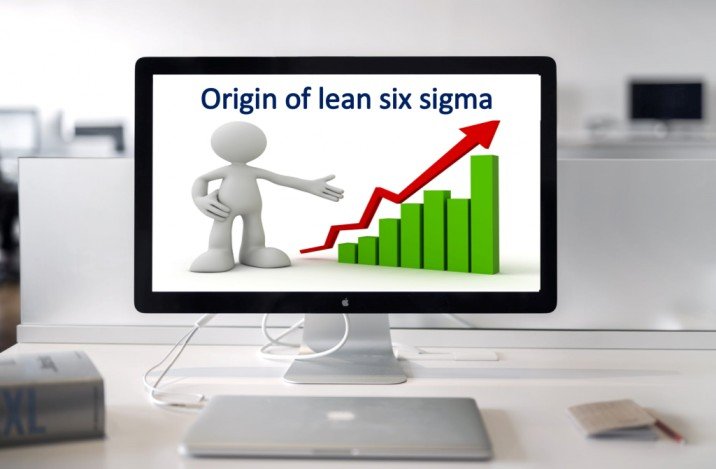
You have seen this most of the time that when people (your friends, family members, you) wants to buy new products like watch, car, mobile, etc, they look for many parameters like brand name, cost, aesthetics, performance and most important is the quality of the product.
People are more interested in the quality of the product which they want to buy so quality defines how satisfied the customers with the product or service.
As a business owner or employee, What do you think about the quality? I think depending on your product, your service, or your business, it can mean any number of things. But at the end, it all boils down to how well we serve the needs of our customers.
Famous author Philip Crosby described quality as, “the conformance to requirements realized through prevention and reduction of defects and nonconformances. ” which means do it right the first time.
There are many paths to sound and robust quality. Two of the most comprehensive and prevalent in the industry are Lean and Six Sigma.
Six Sigma is both a quality management philosophy and also a methodology that focuses on reducing variation, measuring defects, and improving the quality of products, processes, and services.
The purpose of Lean is, to maximize customer value while minimizing waste. So, you can see how Lean and Six Sigma were meant to complement each other.
Evolution of Lean six sigma –
The evolution of Six Sigma began with statistical process control within the quality organization. This developed into business process re-engineering, and later into process improvement philosophy known as Total Quality Management. TQM grew into the methodology we know as Six Sigma. Lean traces its origins to the organization’s desire to improve productivity.
One of the first examples of this, the forward production system, was used to assemble cars. This was used as the basis for the Toyota production system. Just In Time production philosophies combined with the Toyota production system ultimately evolved into Lean.

Now, Lean and Six Sigma are emerging to get the most of both improvement philosophies. Using Lean and Six Sigma tools empower us to eliminate waste and excess cost, reduce variation and defects, and improve our processes and the customer experience in our business.
The Six Sigma methodology is grounded in a process known as DMAIC. DMAIC stands for Define, Measure, Analyze, Improve, and Control. It is primarily used in manufacturing, service, and transactional settings. Under each phase, there are a series of essential steps required.
The purpose of the define phase is to define the problem in the process and provide a compelling business case appropriately scoped complete with SMART goals and linked to a strategic plan.
Read: http://ashwinmore.com/glossary/dmaic/
Then at the measure phase collect process performance data for primary and secondary metrics to gain insight and understanding into root causes and to establish a performance baseline.
In the analyze phase, analyze and establish an optimal performance setting for each X and verify root causes. The aim here is to demonstrate a positive change to the current state of the process through our adjustments.
Then at the Improve phase, identify and implement process improvement solutions. At last, the control phase establishes and deploys a control plan to ensure that gains in performance maintained.
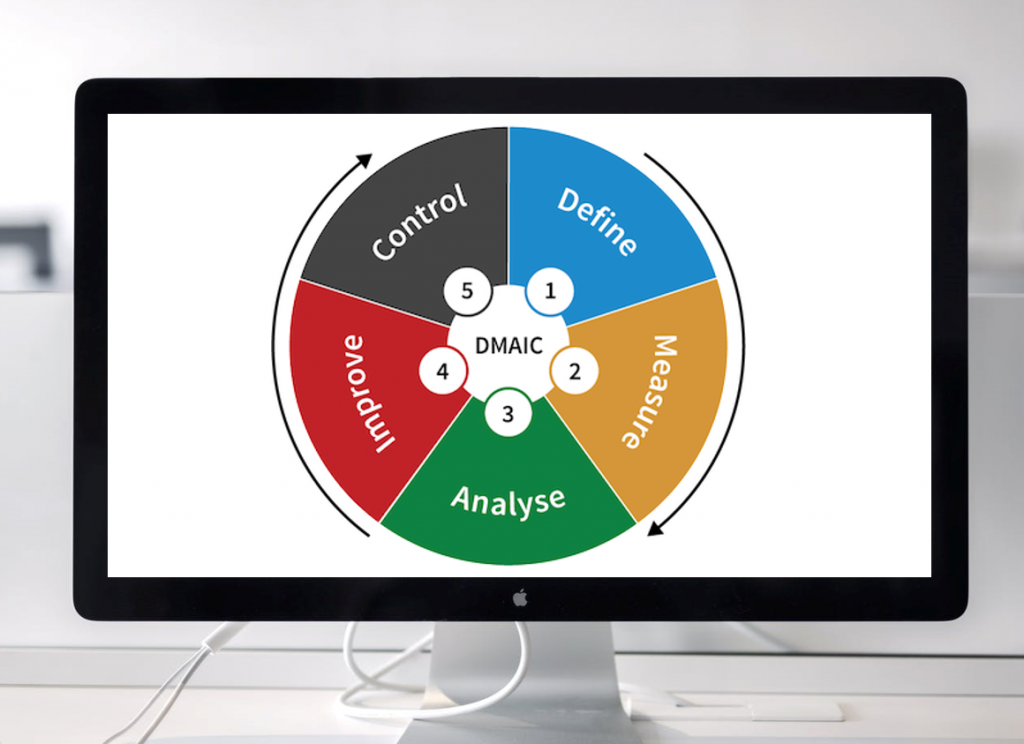
DMAIC cycle
To ensure long term affective change on a larger scale, mechanisms must be put into place to ensure the problem stays fixed long after the team has been re-purposed. The premise behind DMAIC requires a change in our thinking. Instead of being problem-driven, we need to be customer-driven.
Instead of reacting to issues and dissatisfaction, we should search for ways to prevent issues and dissatisfaction. The existence of waste and rework are viewed as opportunities for improvement, prevention, and reduction.
History of six sigma
Six Sigma is a process improvement approach. In Juran’s Trilogy, this falls in the third part, quality improvement. It can also be part of quality planning since it should be strategic. This approach is very focused and follows a five-step model.
There is also a heavy reliance on statistical methods. TQ stands for total quality. It is reflective of Deming’s ideas and embodied in the Malcolm Baldrige criteria. Although there are differences, these two approaches work quite well together.
Total Quality tends to focus on culture change, empowering workers and teams and much of the improvement takes place within the departments or functions. Six Sigma focuses on high-level cross-functional processes, with involvement from upper management and relies on experts to implement.
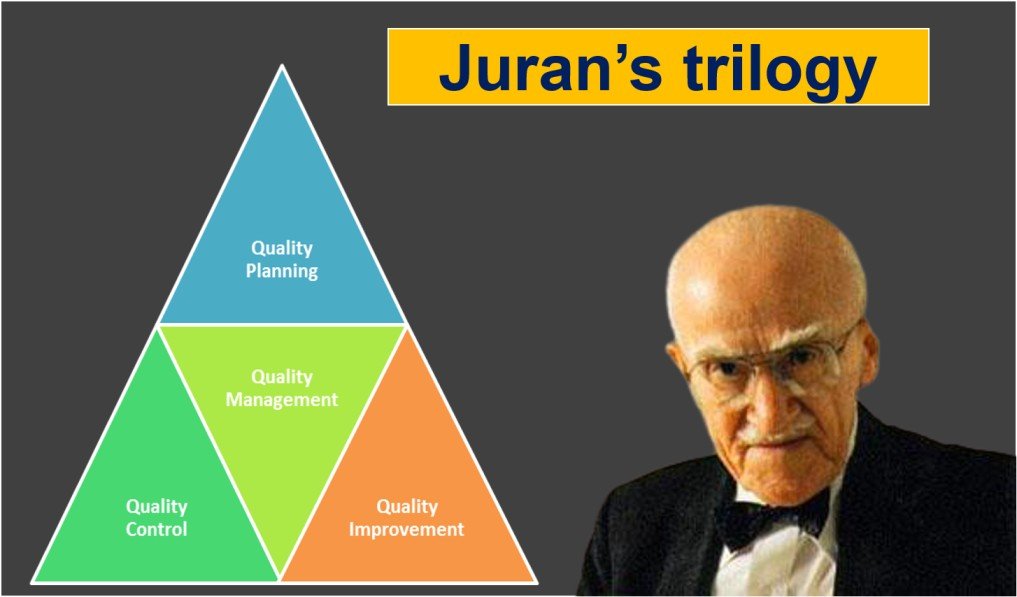
Total Quality generally uses simple tools for process improvement, but these simple tools can be very powerful. You do not need complex statistical methods for everything. It is important to use the approach that fits the situation.
Six Sigma uses a five-step model called DMAIC, to shape improvement projects and focuses on outcomes in terms of benefits for the company. The beginnings of Six Sigma can be traced to Motorola. In the early ’80s in which later transformed into an enterprise-wide strategy for business management and improvement.
Motorola introduced Six Sigma as a measure of quality in 1986. Bill Smith with Mikel Harry developed the initial four-step Six Sigma stages, measure, analyze, improve, and control to reduce defects.
Mikel Harry with Richard Schroeder went on to found Six Sigma Academy in 1994. Mikel Harry is considered the main architect of the Six Sigma movement. The foundations of Six Sigma can be traced to a group of highly knowledgeable individuals in quality.
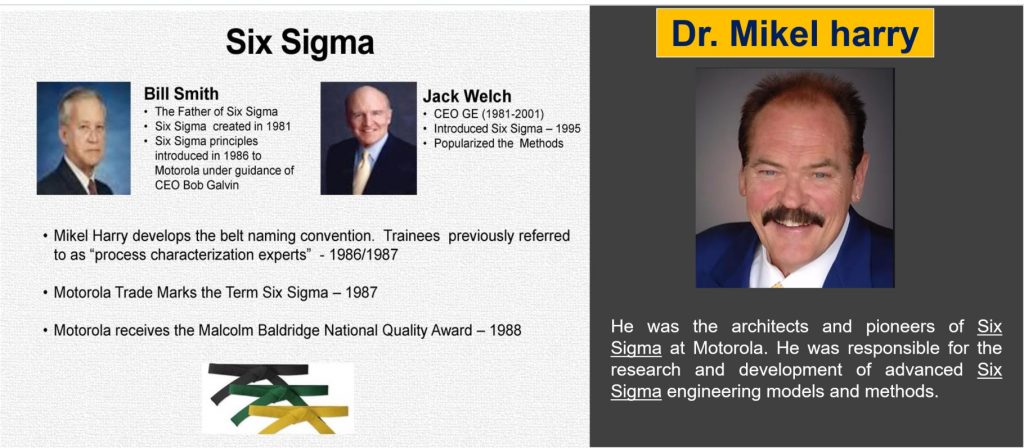
Crosby’s four absolutes for quality conformance and prevention, are high-level statements that help us define and frame the idea of quality within the realm of our business. Dr.Deming is another quality guru who has made substantial contributions to the body of knowledge that we call quality.
These can be summed up as Deming’s 14 points. These include constancy of purpose toward improving, and an unwillingness to accept commonly occurring defects and errors. Deming also strongly opposed inspecting quality in the product and focusing exclusively on price at the expense of quality.
Read: https://www.isixsigma.com/new-to-six-sigma/history/remembering-bill-smith-father-six-sigma/
There is no reason why we cannot have both. If we are strategic. Deming was also a huge proponent of continual improvement at a time when most industries looked to sustain their position in the marketplace as opposed to seizing opportunities for growth.
This continual improvement also reflected in terms of training, training on the job, cross-training, and confirming that training is still valid. Deming also points to the difference between supervision and leadership, and the need to drive fear out of the organization. If an organization is driven by fear, it will never achieve and grow.
Quality gurus:
Dr.Deming also believed in keeping the message simple in the organization, breaking down barriers, and building cross-functional teams from all areas of the business. Deming was not very enthusiastic about numerical quotas for the workforce or numerical goals for the management. Even today, every organization has a difficult time moving away from the need for numerical metrics as a means of tracking performance.
He also had little use for merit systems and annual ratings, and instead felt that these mechanisms fed into employee fear and created an environment of competitiveness instead of collaboration.
Finally, in line with his ideas of continuous improvement, Deming envisioned an organization heavy into the education and self-improvement of every employee.
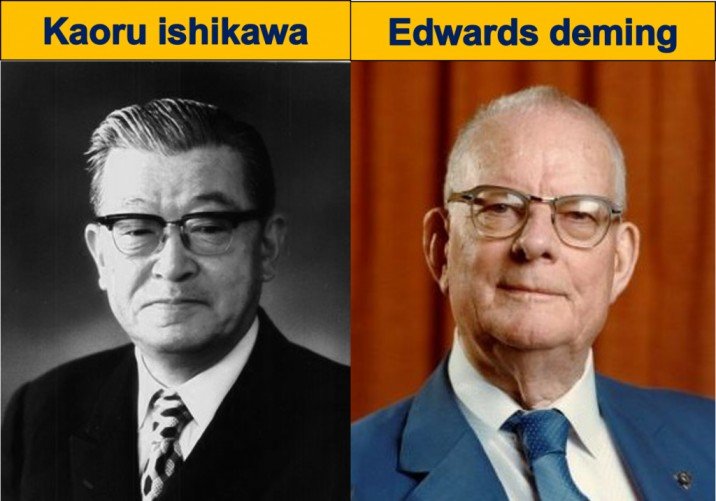
Employees are the organization’s most valuable asset. They should be treated as such. Once you have raised the level of knowledge of your employees, utilize them and everyone to transform your business. Too often, organizations have segments of their employee population that go unutilized or underutilized.
Taguchi was another quality guru who recognized the importance of initiating the proper quality at the engineering and design levels of the process.
Feigenbaum had some similar yet distinct insights into quality beyond the manufacturing floor. By focusing our quality efforts in the design and delivery realms, we can see gains in areas outside the scope found on the manufacturing floor.
In summation, Feigenbaum characterized total quality control as an effective system for integrating the quality development, quality maintenance, and quality improvement efforts at the most economical levels.
Other contributions found in various stages of the Six Sigma process come from Ishikawa, who is known for the Fishbone diagram and the Five Whys.
Once we have established the causes, Shewhart took things forward to identify assignable and chance causes. These causes can be monitored through statistical process control and confirmed through PDCA, Plan, Do, Check, Act.
Another luminary in quality circles is Juran, we already talked about him. Juran’s most significant contribution is known as Juran’s Trilogy. This includes quality planning, quality control, and quality improvement.
If you like this article please share and subscribe. I will meet you in the next article.
Very good information regarding the history of Six Sigma.